As biomass combustion is relatively new, automation logic embedded in the hardware is frequently inefficient and needs continuous optimization by the operators to reach the efficiency of traditional gas-burned boilers. Ωpera can be used to surface all the control parameters to the web, allowing the operators to automate and optimize the setpoints in a transparent and easy way.
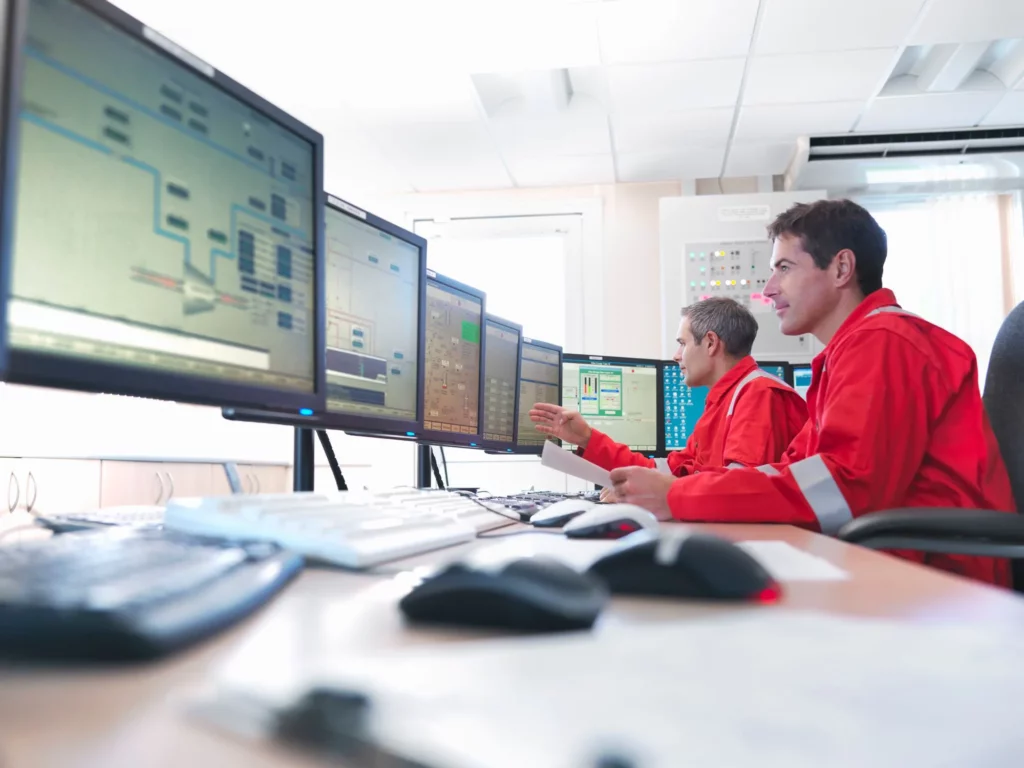
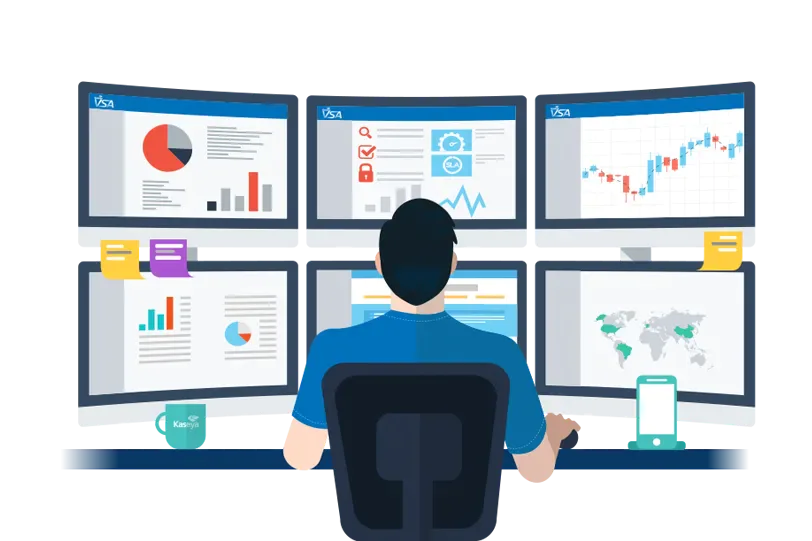
Ωpera
Empower your industrial processing operations with Ωpera, Koidra’s operator-driven automation platform.
Benefits to operators
Operators-led automation.
Production operators and managers are in control, allowing them to advance their automation strategies in a limitless way without being limited by dead code or interfaces.Revolutionize the way you run your production facility with a modern automation approach. The traditional model of automation, where operators are limited to following static instructions embedded in blackbox hardware, is outdated. The real experts in process flow and optimization are the operators, and they understand better than anyone what needs to be automated and how to improve control strategies.
With the advent of low-code development and other modern software/hardware technologies, business users can now easily program and evolve their automatable tasks. Say goodbye to the outdated operators-slave automation model and embrace a new era of operator-driven automation.
A typical control room setup. Controllers frequently have to follow the screens and manually change setpoints. Whole-system optimization.
Integrate and optimize siloed systems in a holistic way for optimal performance.Whole-system optimization is a critical aspect of modern automation. Ωpera provides a comprehensive platform that enables businesses to easily integrate and optimize siloed systems, resulting in optimal performance and improved efficiency. With Ωpera, you can streamline your operations by eliminating the need for manual intervention, reducing downtime and maximizing output.
Additionally, Ωpera’s holistic approach enables operators to have real-time visibility into all aspects of the production process, allowing for the identification of inefficiencies and the implementation of corrective measures. This results in a more productive, agile, and flexible production facility, with the ability to respond quickly to changes in demand and market conditions.
By integrating and optimizing siloed systems, Ωpera enables companies to achieve a level of performance and efficiency that was previously unattainable.
Institutionalized know-hows.
Ωpera enables the preservation and transfer of production and maintenance know-how, ensuring it remains an asset of the company rather than being tied to individual experts.With Ωpera, operators and managers can preserve and transfer valuable production and maintenance know-how, ensuring that the knowledge remains an asset of the company and is not lost when individual experts retire or leave the company.
By enabling the preservation and transfer of institutionalized knowledge, Ωpera ensures that companies can build upon the accumulated knowledge of their employees and improve their operations over time. This enables companies to maintain a competitive edge and improve their bottom line.
In addition, Ωpera provides a collaborative environment for operators and managers to share their expertise and learn from one another. This fosters a culture of continuous improvement and learning, driving the company forward and enabling it to stay ahead of the competition.
Kaizen booster.
Enable operators to iterate and improve control strategies, driving continuous improvement and increasing yield, efficiency, and competitiveness.The principle of Kaizen, or continuous improvement, is a driving force behind many successful companies. With Ωpera, operators have the tools they need to drive Kaizen and continuously improve their control strategies.
Ωpera empowers operators to iterate and experiment with new control strategies, enabling them to optimize production processes and improve yields, efficiency, and competitiveness. The platform provides a flexible and user-friendly interface, allowing operators to easily program and evolve their automatable tasks, without being limited by dead code or outdated interfaces.
By enabling operators to drive continuous improvement, Ωpera helps companies to stay ahead of the curve and maintain a competitive edge. Whether it’s improving yields, reducing downtime, or streamlining processes, Ωpera’s Kaizen booster is a powerful tool for achieving greater success in your industrial operations.
Benefits to solutions integrators
Flexibility.
Ωpera's user-friendly interface and low-code development platform allows solutions integrators to quickly and easily program and customize the automation solution to meet the specific needs of their customers, regardless of the size or complexity of the project.For perspective: software engineering and computing in general have evolved rapidly in the last 50 years. Today, no one would program in assembly when developing applications. In contrast, ladder logic and PLC programming have stayed the same.
Scalability.
Traditional automation requires repetitive reprogramming for new industrial development projects — which defeats the core purpose of automation. With Ωpera, you just need to install and configure, not reprogram, for each new project. This enables you to reduce both the time and costs of deploying an automation solution to your customers.
Select Features
Web-based programming.
With Ωpera, business users can read and update automation logic on a web browser, from anywhere. Despite the ease of programming, rest assured that your code is compiled, optimized, and can run on-premise. This ensures safe operations, even when the internet is not available.Formula-based Control.
What if automation programming is as easy as writing formulas in Excel.The user interface allows linking a setpoint to an Excel-like formula. In the formula, acquired sensor data can act as inputs and combine with built-in Excel functions / customized functions to give the desired control output in different operational scenarios. This low-code language is expressive and enables the development of strategies ranging from simple to sophisticated. Version Control.
What if you can track all the changes made to the system and can restore to a version at any time?
Case Studies
Greenhouse’s climate control
Ωpera has been deployed to control the climate of commercial greenhouses, in ways that traditional climate computers are ineffective.
A demo application in greenhouse’s climate control. Warning: commercial deployments are not shown publicly. Biomass dryer control
Deployment of dryer control for a biomass production facility. In this deployment, Ωpera adds an additional layer of automation on top of the existing PLC by automating the dryer and burner’s control setpoints. They no longer need to tune these parameters repeatedly. In addition, this enables the facility to further optimize the automation for higher drying efficiency. Biomass boiler control
Biomass boilers are emerging as an ideal solution for carbon-neutral and cost-effective heat and power generation at industrial processing facilities. They’re a proven alternative to boilers fueled by natural gas, the cost of which has been skyrocketing in recent years. However, controlling biomass boilers effectively, for high throughput and high energy efficiency is not easy. Operators frequently have to learn how to mix and process input materials of different moisture and particle sizes, and control the air pressure, fan speed, flue gas treatment, etc. in different ways.